Understanding the Fabrication Process: From Concept to Completion
Introduction to Fabrication
Fabrication is a critical process in the creation of countless products used in everyday life, from household items to complex machinery. Understanding this process provides insight into how raw materials are transformed into finished products. Whether you're a curious consumer or a professional in the industry, knowing the steps involved can enhance your appreciation for the skill and technology required.
The fabrication process involves a series of steps that take a product from concept to completion. Each stage is crucial in ensuring the final product meets the desired specifications and quality standards. From initial designs to the final touches, fabrication is a blend of art and science.
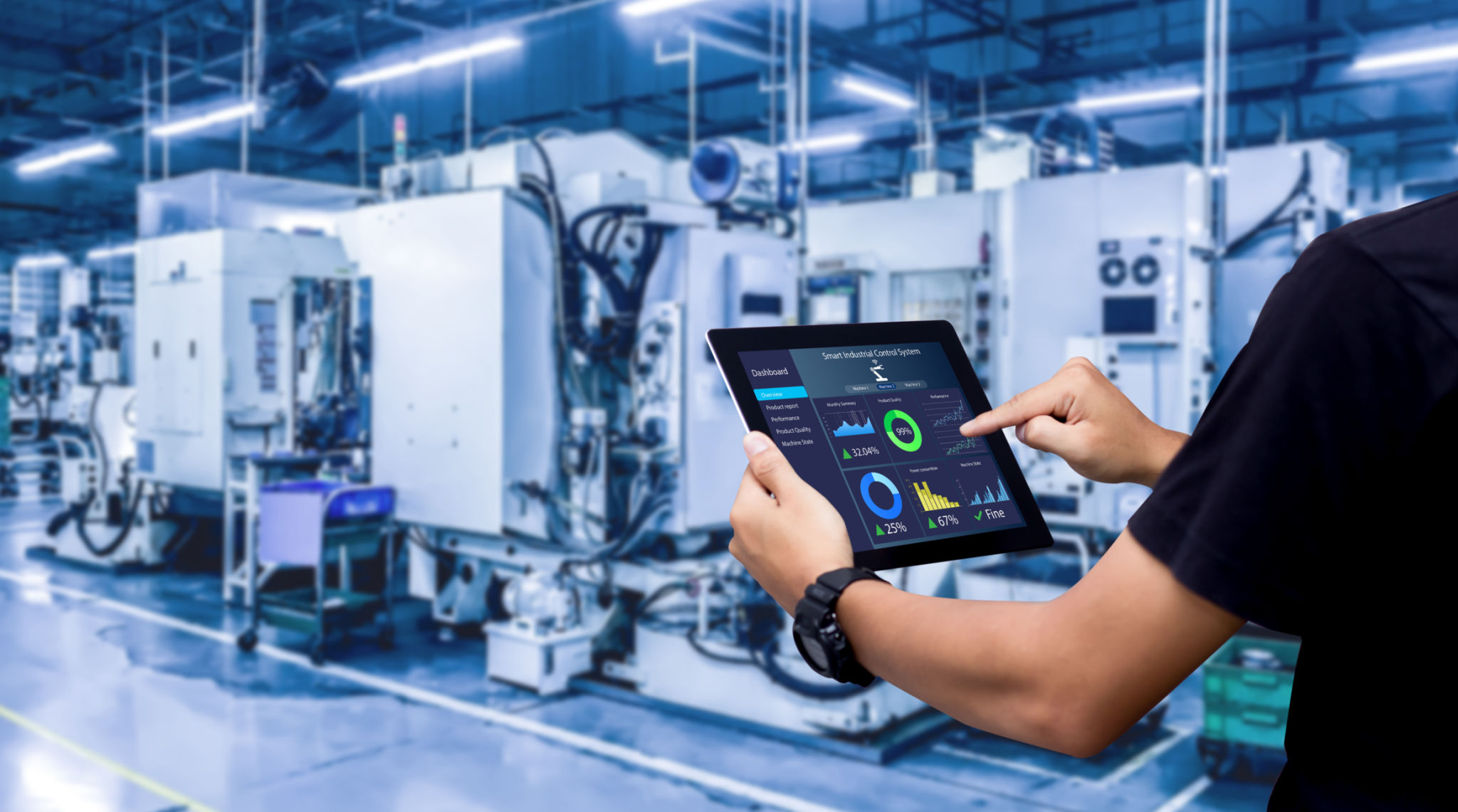
Conceptualization and Design
The first step in fabrication is conceptualization. This involves brainstorming ideas and creating initial designs. Designers and engineers work together to draft blueprints and 3D models. These models are essential for visualizing the final product and determining the necessary materials and processes.
During the design phase, it's important to consider factors such as functionality, aesthetics, and cost-effectiveness. Advanced software tools aid in refining designs and performing simulations to predict how the product will behave under real-world conditions.

Material Selection
Choosing the right materials is a pivotal part of the fabrication process. The selection depends on the product's intended use, required durability, and cost constraints. Common materials include metals, plastics, composites, and ceramics. Each material has its unique properties that must be considered during selection.
Material selection impacts not only the product's performance but also its manufacturability. Engineers must ensure that the chosen materials can be effectively processed using available fabrication techniques.
Manufacturing Process
Once the design is finalized and materials are selected, the manufacturing process begins. This can involve various techniques such as cutting, welding, molding, and assembling. Each method is chosen based on the material properties and desired characteristics of the final product.
Quality control measures are integral during manufacturing to ensure each component meets specifications. Precision and accuracy are crucial to avoid defects that could compromise product integrity.

Assembly and Finishing
After individual components are manufactured, they are assembled into the final product. This stage may involve additional processes such as painting, polishing, or coating to enhance appearance and functionality.
The finishing touches are what transform a collection of parts into a complete, market-ready product. Attention to detail during this phase ensures that the product not only functions well but also meets aesthetic standards.
Quality Assurance and Testing
Before a product is deemed ready for market, it undergoes rigorous quality assurance and testing. This ensures that it performs as expected and meets all safety and regulatory standards. Tests may include stress testing, thermal analysis, and endurance trials.
Quality assurance is not just about catching defects but also about ensuring continuous improvement in the fabrication process itself. Feedback from testing can lead to design modifications or process enhancements.
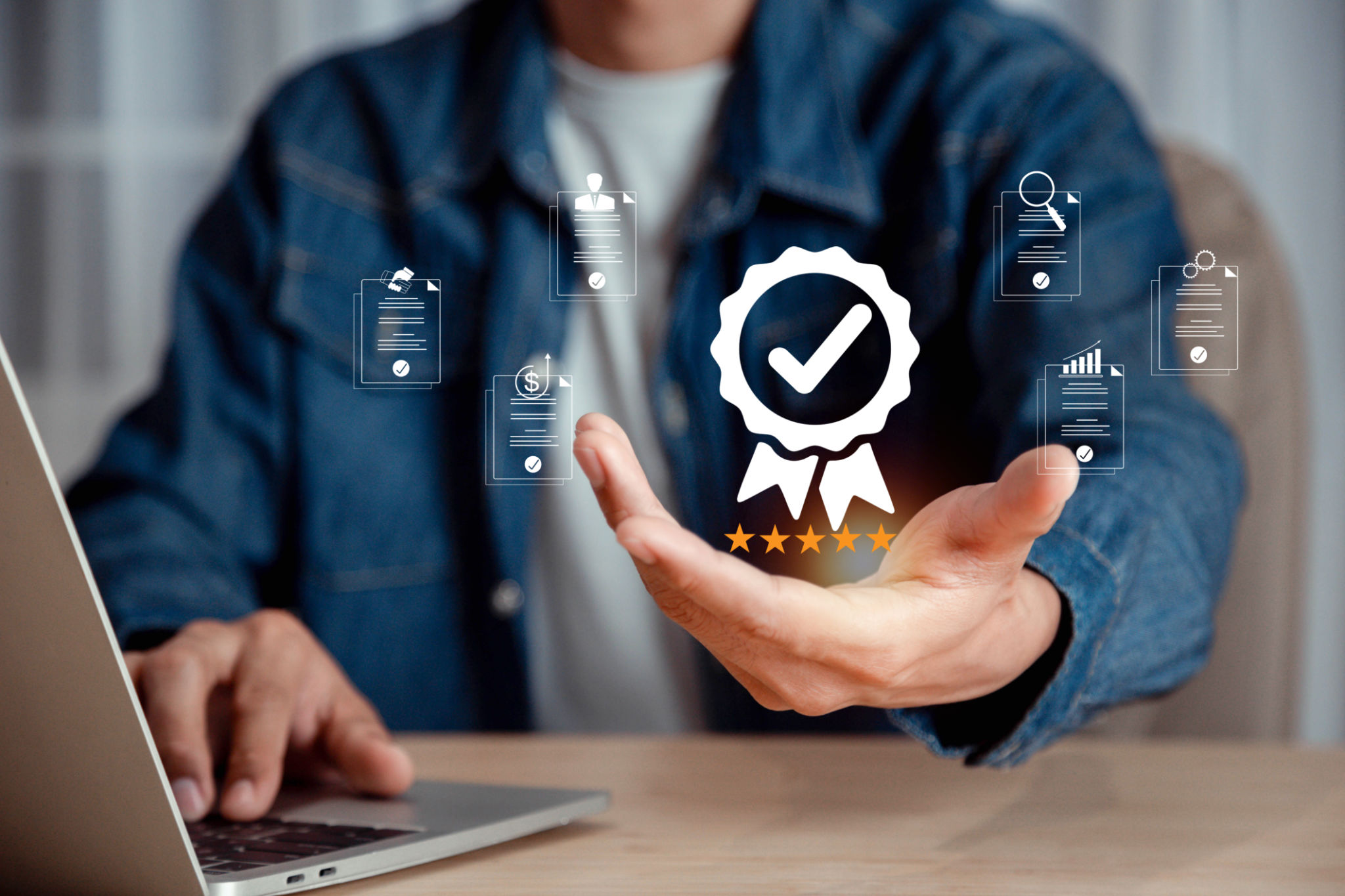
Conclusion: From Vision to Reality
The fabrication process is a journey from concept to reality, involving multiple stages that require precision, creativity, and expertise. Each step builds upon the previous one to create products that are both functional and aesthetically pleasing.
Understanding this complex yet fascinating process highlights the importance of collaboration among designers, engineers, and technicians. It showcases how innovative ideas can be transformed into tangible products that enhance our daily lives.