Debunking Common Myths About Welding and Fabrication
Misconceptions About the Safety of Welding
One of the most common myths about welding is that it is inherently unsafe. While it is true that welding involves certain risks, proper safety measures can significantly mitigate these dangers. Personal protective equipment (PPE) such as helmets, gloves, and protective clothing are essential to ensure a safe working environment. Additionally, modern welding technology has advanced to incorporate safety features that further protect welders.
Another misconception is that only extreme heat is a concern in welding. In reality, welders must also be cautious about exposure to fumes and gases. Proper ventilation systems and fume extractors are crucial in maintaining air quality and preventing respiratory problems.
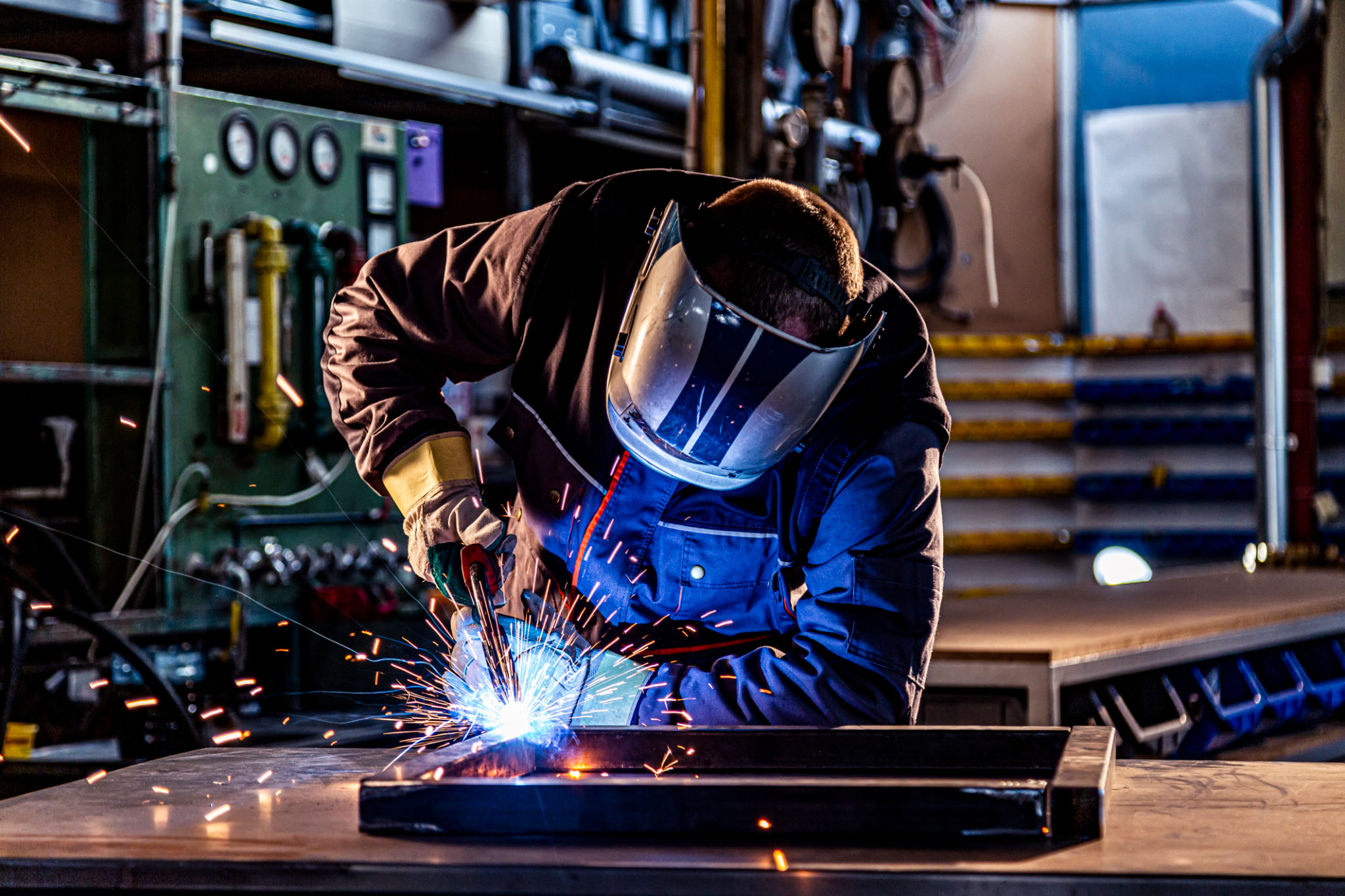
The Myth of Limited Applications
Many people believe that welding and fabrication are limited to construction and heavy industries. This could not be further from the truth. Welding plays a critical role in a diverse range of sectors including automotive, aerospace, and even in the creation of art installations. The versatility of welding techniques allows for applications in both large-scale industrial projects and intricate, detail-oriented work.
Welding's flexibility extends to the materials it can join. Beyond traditional metals like steel and aluminum, welders can work with materials such as titanium, copper, and even plastics using specialized techniques. This adaptability makes welding an essential skill in various fields.
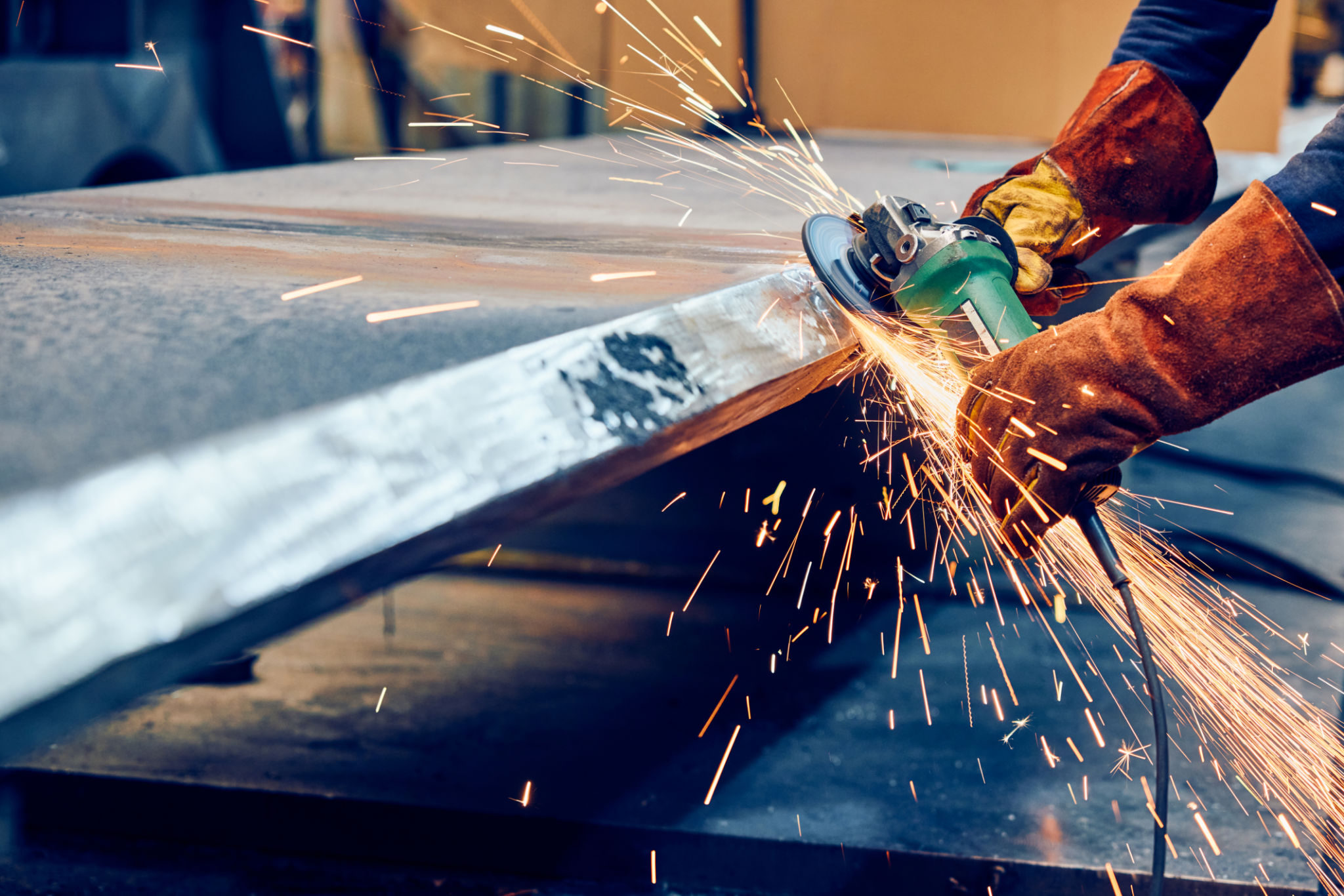
Skilled Labor vs. Automation
A prevalent myth is that automation will soon replace human welders entirely. While automation has transformed many industries, welding still heavily relies on skilled labor. Automated systems are excellent for repetitive tasks and mass production, but they lack the adaptability and problem-solving skills of a human welder.
Human welders are indispensable for tasks that require intricate craftsmanship or quick adjustments to unforeseen issues. Their ability to apply precision and creativity remains unmatched by machines. Rather than replacing welders, automation serves as a tool to enhance their capabilities and efficiency.
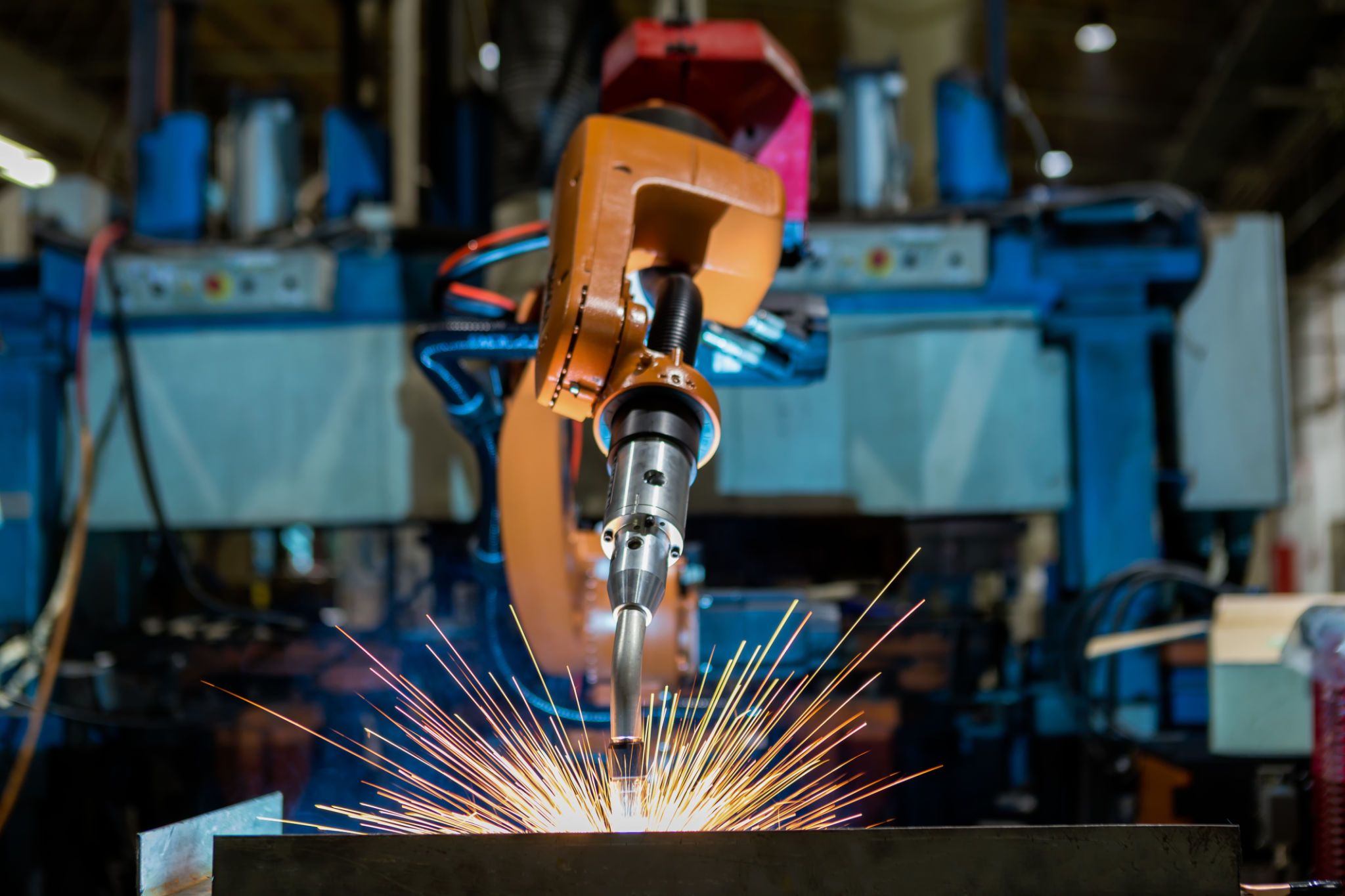
The Cost-Effectiveness Misunderstanding
Some individuals mistakenly view welding and fabrication as prohibitively expensive processes. In truth, advancements in technology have made these services more cost-effective than ever before. Newer welding methods can reduce material waste and increase the speed of production, leading to savings for both businesses and consumers.
Moreover, investing in quality welding work can lead to long-term savings by ensuring durable and reliable products. This reduces the need for frequent repairs or replacements, ultimately proving more economical over time.
The Myth of Simplicity
A common misconception is that welding is a simple task that anyone can pick up quickly. While basic welding techniques may be accessible to beginners, mastering the craft requires extensive training and experience. Professional welders undergo rigorous education to understand different materials, techniques, and safety protocols.
The complexity of welding lies in its precision and attention to detail. Achieving a perfect weld involves understanding the properties of the materials involved, selecting the appropriate technique, and executing it with skill. This level of expertise is why professional welders are highly valued in their field.