Case Study: How Oaks Engineering Delivered a Custom Fabrication Solution
Understanding the Client's Needs
Oaks Engineering has long been known for its innovative approaches to engineering challenges, but this particular project highlighted their ability to tailor solutions to specific client needs. The client, a large-scale manufacturing company, was facing repeated production delays due to inefficient and outdated equipment. They required a custom fabrication solution that would not only resolve these issues but also improve overall operational efficiency.
After an initial consultation, Oaks Engineering conducted a comprehensive site assessment. This assessment was crucial in identifying the bottlenecks in the client's production line. The key objectives were clear: enhance productivity, ensure reliability, and integrate seamlessly with existing systems.
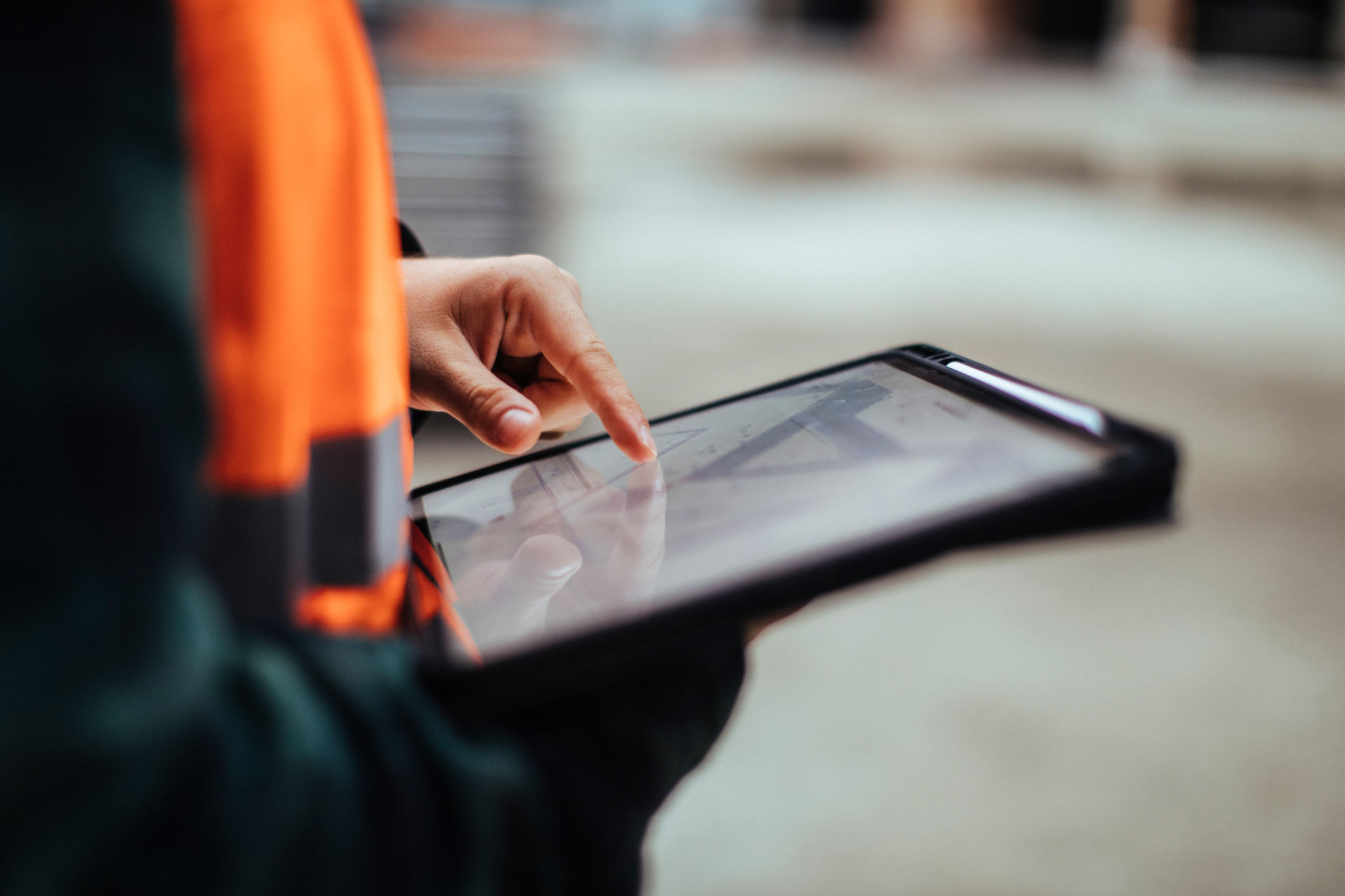
Designing a Tailored Solution
With a clear understanding of the client's challenges, Oaks Engineering’s team of experts got to work designing a custom fabrication solution. The design phase involved close collaboration with the client to ensure that the final product would meet all expectations. They used advanced CAD software to create detailed models and simulations, allowing the client to visualize the proposed solution.
The solution involved redesigning key components of the production line. This included fabricating new machinery parts that were specifically tailored to fit the client's operations. By focusing on precision and quality, Oaks Engineering ensured that these parts would provide superior performance and durability.

Implementation and Testing
Once the design was approved, the fabrication process began. Oaks Engineering leveraged its state-of-the-art facilities to manufacture the custom components. Throughout this process, quality control was paramount. Each piece underwent rigorous testing to ensure it met the highest standards.
The installation phase was carefully planned to minimize downtime. Oaks Engineering's team worked efficiently, coordinating with the client's staff to integrate the new components seamlessly into the existing system. Post-installation, thorough testing was conducted to ensure optimal performance.
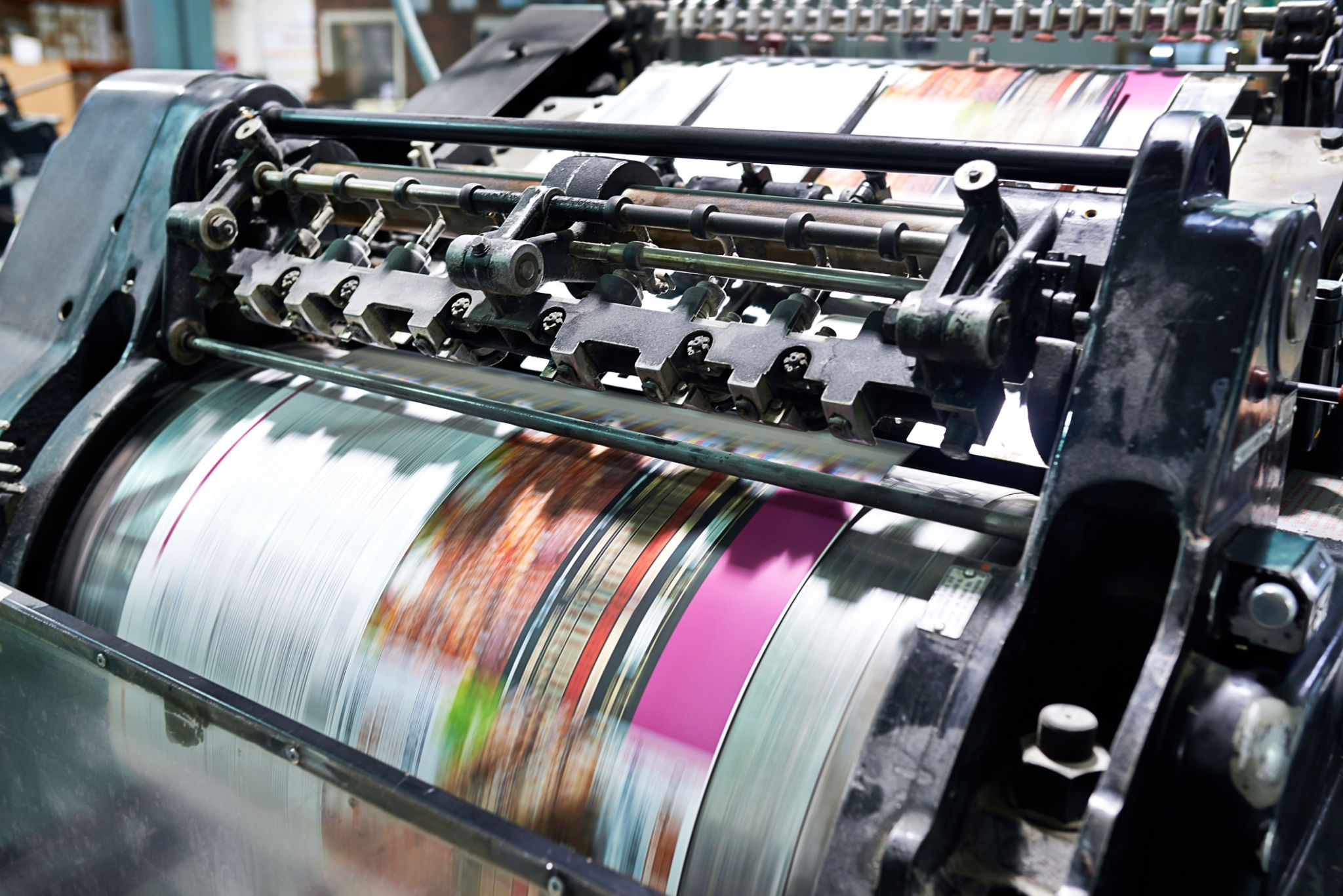
Results and Client Feedback
The results of the project were impressive. The custom fabrication solution not only resolved the initial issues but also enhanced the overall efficiency of the production line by 30%. This significant improvement led to increased output and reduced costs for the client.
The client expressed their satisfaction with both the process and the outcome. They appreciated Oaks Engineering’s dedication to understanding their specific needs and delivering a solution that exceeded expectations. This project exemplified how customized engineering solutions can drive substantial business improvements.
Lessons Learned
This case study highlights several key lessons for businesses seeking custom engineering solutions:
- Comprehensive assessment of current systems is critical to identifying real issues.
- Collaboration between engineering teams and clients ensures that solutions are both effective and practical.
- Quality control and testing are essential in delivering reliable products.
Oaks Engineering continues to leverage these insights in future projects, maintaining its reputation for excellence in custom fabrication solutions.
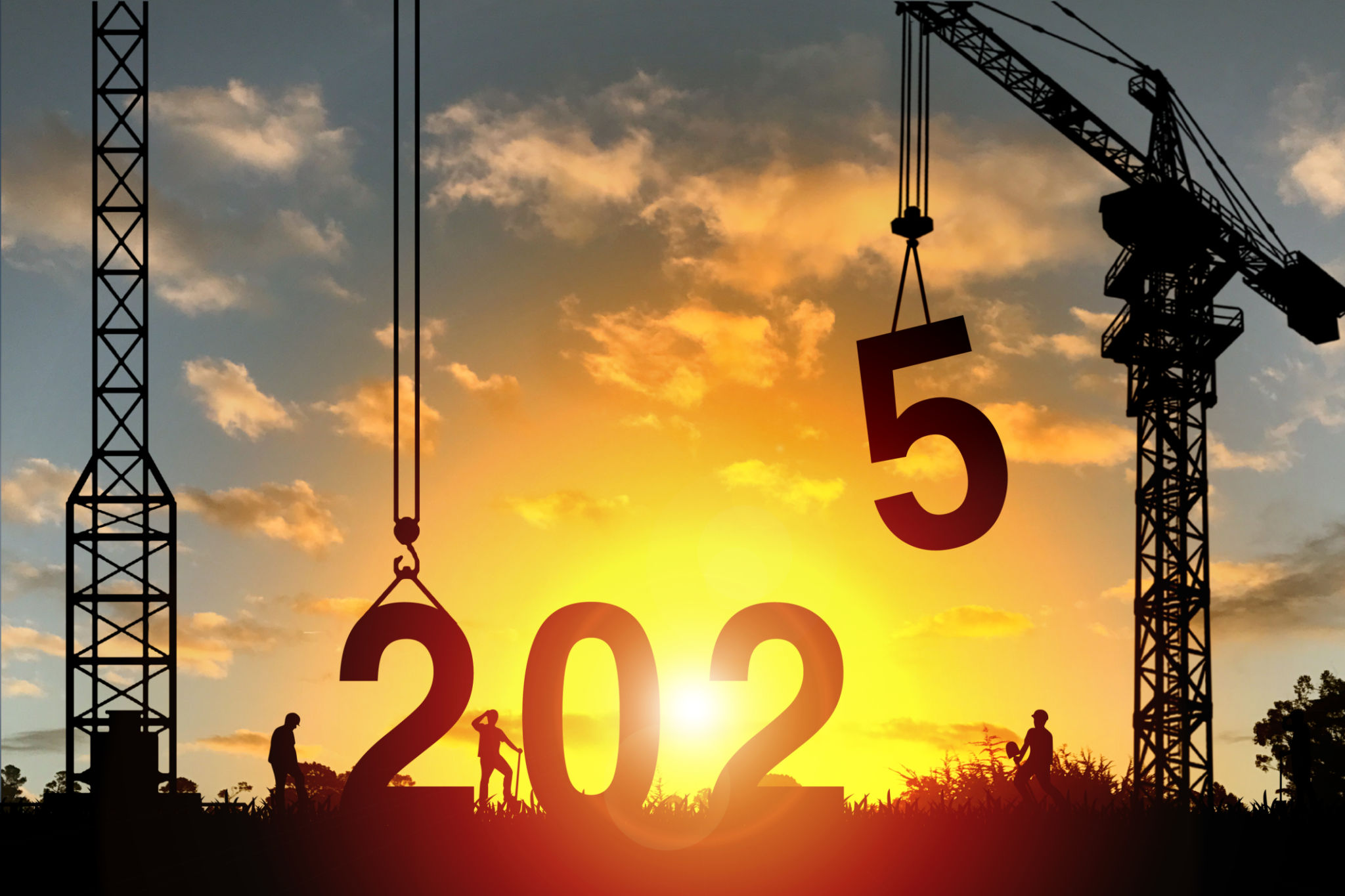